All docks need maintenance, especially over time due to constant use. Addressing issues promptly can prevent minor problems from escalating into major systems failures, saving businesses from unnecessary repair costs and potential safety risks.
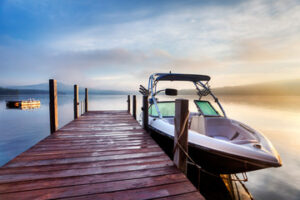
Dock Repair usually starts with a visual or professional inspection of the dock’s floats, planks and railings. If significant damage is noted, it may be time for a complete dock replacement.
Floats can be damaged by water, weather or debris. Whether they are moored, buoyed or tied down, the damage can be costly to the ship’s owner and operator. A damaged float can be a serious problem that needs to be repaired as quickly as possible. The Member, master and crew of the Ship can be held liable to pay for various kinds of damages to fixed and floating objects, including natural habitat resources with direct or derived economic value which have been physically damaged by physical contact with the Ship, and for restoration costs and other natural resource damages. Cover for such liabilities is not available as of right under Rule 37, but may be covered by hull policies on standard terms.
Foundation Deterioration
When your home’s foundation begins to show signs of deterioration, it’s important to act quickly. Foundation issues can lead to a variety of problems, including cracking floors and walls, water leaks, musty odors in the basement or crawl space, and pest infestations.
Some homeowners are tempted to simply cover up the cracks with caulk or epoxy, but this is only a short-term fix. Filling in a crack doesn’t address the cause of the problem, which is often rooted in the soil conditions around your home.
Depending on the cause of the problem, it may be necessary to excavate and rebuild your foundation. This is typically a large-scale job that can cost tens of thousands of dollars or more. A non-invasive option is piering, which uses steel posts to bolster the foundation and stabilize it. This is a less expensive alternative to excavation.
If you notice any of the early warning signs, call a licensed professional right away. They will be able to recommend the best repair solution for your particular situation.
Foundation damage can have a major impact on your house, causing serious structural problems that are costly to fix. If left unattended, these problems can also worsen and affect other parts of your home.
One of the most common problems is sinking or bowing in the foundation walls. This can be caused by poor drainage or soil erosion that causes moisture to accumulate near your foundation. In most cases, this is a sign that the soil hasn’t been properly graded and that it is sinking into place.
Another common problem is hydrostatic pressure from the soil above your foundation. This pressure can cause horizontal cracking in the concrete. It can be exacerbated by heavy equipment like bulldozers or earth rollers that create a stronger force than the foundation was designed to handle.
Sometimes a concrete mix contains a mineral called expansive pyrrhotite, which can cause your foundation to crack. Symptoms of this problem include hairline cracks in the foundation walls that widen as the concrete expands. You may also see a rust color residue or white powder on the walls. This type of cracking is not reversible and requires replacement of the concrete with a new mixture that doesn’t contain pyrrhotite.
Weathered Wood
As wood ages, it loses its strength and its color fades, leaving a dull, weathered appearance. This is a natural process that can lead to the degradation of wood furniture, but with a little effort, it can be restored and repurposed into something new. In this blog post, we’ll discuss how to restore weathered wood and share some helpful tips for making the project a success!
Before beginning, it is important to understand the difference between weathering and decay. Decay is caused by fungi that live in the wood, and it requires a constant source of moisture to thrive. Weathering, on the other hand, is an environmental phenomenon that is largely caused by sunlight. Sunlight causes a series of chemical reactions to occur in the wood, which eventually alters its appearance.
Once the wood has been treated with the right products, it can be restored to its original beauty. To make this happen, the wood must be thoroughly inspected before beginning any work. The inspector should note any significant damage like deep cracks or warping as well as any areas that are showing signs of rot. After a careful inspection, the wood should be cleaned and prepared for the refinishing process.
There are several different products available that can be used to clean and prepare the surface of weathered wood for refinishing. For example, the Benjamin Moore Restore (316) product is ideal for restoring severely weathered wood. This product is bleach-free and safe to use on decks, fences, siding, and other outdoor surfaces. It is also suitable for removing moderate to severe mildew and mold growth.
While there are some companies that offer “pre-weathered” wood, the integrity of these boards is often compromised during this process. They are typically laid horizontally and left to weather for a year or more, which can result in severe twisting, cupping, bowing and other defects. Additionally, these boards can harbor mold and mildew, a major health hazard to homeowners.
Our pre-weathered design replicates the look of textured wood that has been exposed to years of weathering and aging. This is the perfect option for creating an aged and rustic appearance on any exterior or interior projects! It is available in our Circle Sawn design and milled to 1×12 lengths of 2-12′ with tongue and groove and blind nail application.
Damaged Railings
If a part of your dock’s railing becomes damaged, it is important to address the issue as soon as possible. The safety benefits that the barrier provides are diminished when a single section of it is no longer functional. It is also more dangerous to walk near a fence that isn’t fully intact, and this can lead to serious injuries.
Regular inspections can spot many early warning signs that your dock’s railing is deteriorating and in need of repair. Routine inspections also help to ensure that your dock is up to OSHA standards for stairway railings, which are highly regulated. If a guardrail fails inspection, governing bodies will typically detail why in a written report that building maintenance staff can use to guide their repair efforts.
Wooden railings can be particularly vulnerable to damage. Termites, carpenter ants, and other pests can tunnel through the materials and hollow them out from the inside. This can leave the railing structurally weak, so it is important to treat any sign of bug infestation as quickly as possible.
It is also a good idea to inspect wooden railings frequently for rotting. The wood may feel spongy or moist, or you might notice that it has dark spots in the grain that are deeper than usual. If you do observe rot, you will need to replace the affected portions of your dock’s railing.
Metal railings are also susceptible to rust and corrosion, which can weaken them over time. You can minimize this risk by treating your railings with a protective coating. In addition to protecting the metal, this coating can make it easier to remove stains from the surface of your deck or dock.
Lastly, consider examining the anchors that hold your railing in place. If they are loose, you can re-embed them in concrete using commercially available epoxy. You will need to choose slightly larger anchors than the ones that were originally embedded in the concrete, so take a trip to your local hardware store and purchase some new fasteners.
After you’ve removed the damaged sections of your dock’s railing, clean the remaining pieces with a wire brush to remove any loose debris. Then, tape off the area where you’ll be putting in the new screws, and use a hammer drill with a masonry bit to remove the old anchors. Afterwards, use pliers to extract any sharp pieces of rusted metal that are left behind in the holes.